wirtualizacja
No images found in specified folder.
Looked for images in: "2018"
Under your root image folder: "images/galeria"
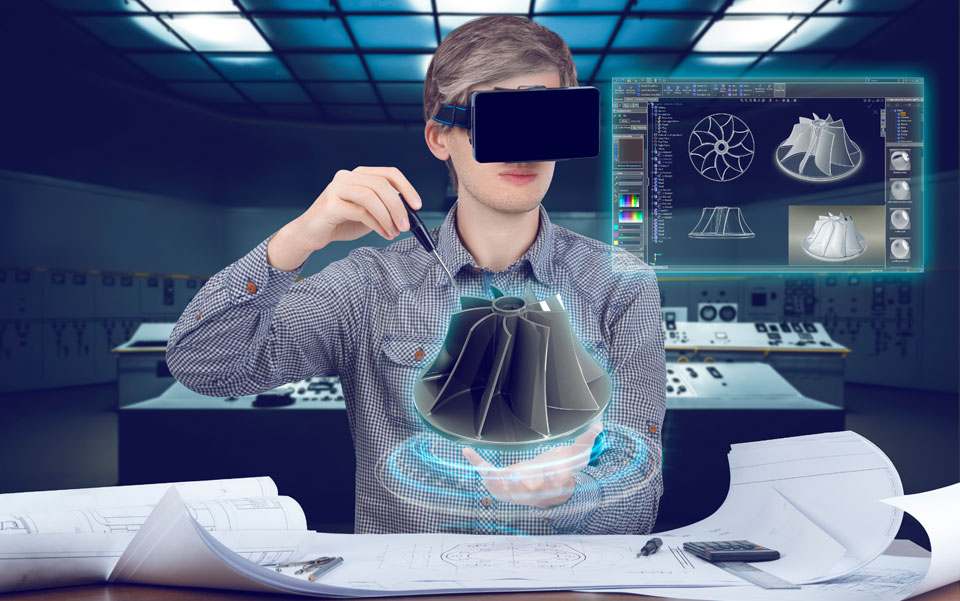
Jednym z kluczowych elementów wdrożenia systemów zarządzania przedsiębiorstwem jest zapewnienie odpowiednio wydajnej i kompleksowej akwizycji danych z fazy projektowania wyrobów. Wytwarzanie wyrobów wymaga stworzenia struktur wytwarzania, marszrut procesów oraz dokumentacji produkcyjnej. Bardzo często proces tworzenia dokumentacji i czas jej powstawania jest dużym ograniczeniem.
Niniejszy artykuł obejmuje analizę możliwości integracji współczesnych systemów CAD i PDM z systemem Rekord.ERP. Zakres obejmuje zarówno automatyczne pozyskanie danych, jak i możliwości wykorzystania elektronicznej formy dokumentacji w operacyjnym zarządzaniu produkcją.
Od dłuższego czasu firmy działające na współczesnym rynku zmuszone są do oferowania szerokiej gamy produktów, tak, aby spełnić wysokie i często zmienne wymagania klienta. W wielu przypadkach skróceniu uległy również czasy oczekiwania klienta na wyrób. Klienci stali się bardziej wymagający i chcą zaspokojenia swoich indywidualnych potrzeb. Zamiast produkcji masowej, obecnie przedsiębiorstwa zmagają się z produkcją jednostkową i małoseryjną. Dla wielu przedsiębiorstw oznacza to konieczność produkcji, w krótkich cyklach przy zachowaniu spełnienia kryterium kosztowego. Ze względu na indywidualne potrzeby klientów, często istnieje potrzeba konstrukcyjnego projektowania wyrobów. Obecnie realizowane jest to w większości za pomocą narzędzi CAD. Po wykonaniu projektu konstrukcyjnego, należy opracować procesy wytwarzania i później je zrealizować. W tym celu wykorzystywane są systemy zarządzania klasy ERP. Klient jest coraz bardziej wymagający i oczekuje szybkiej odpowiedzi, zarówno na zapytanie ofertowe, jak i na gotowy wyrób.
Projektowanie produktu
klasy PC i instalowane na nim systemy użytkowe CAD stały się powszechne w zastosowaniach inżynierskich. Kolejnym etapem była, więc ich integracja funkcjonalna, która po pewnym czasie stała się integracją procesowo zorientowaną, a więc ukierunkowaną przede wszystkim na rozwój i wytwarzanie danej klasy produktów. Do rozwoju wymiany informacji o wyrobie, w sposób strukturalny, przyczynił się również rozwój sieci kooperacyjnej wśród poddostawców w przemyśle motoryzacyjnym. Każdy z dużych koncernów samochodowych kooperuje z dużą grupą poddostawców zmuszanych do przejmowania i wdrażania koncepcji producenta wyrobu finalnego w sposób elastyczny, szybki, profesjonalny i efektywny.
Systemy bazodanowe w obszarze TPP
Moduły zarządzania produkcją występujące w systemach transakcyjnych można rozpatrywać w rozbiciu na dwie części: statyczną, będącą swoistą bazą know-how firmy i dynamiczną odpowiedzialną za obszar planowania i zarządzania operacyjnego. Baza know-how firmy przechowywana jest w modułach Technicznego Przygotowania Produkcji stanowiących integralną część systemów klasy ERP lub też będących autonomicznymi rozwiązaniami Kartoteki Technicznego Przygotowania Produkcji, które gromadzą i zarządzają informacją o tym, z czego poszczególne wyroby są zbudowane (czyli dane dotyczące struktury wyrobów) oraz tego w jaki sposób należy je wykonać (czyli dane dotyczące operacji procesu wytwarzania – marszrut technologicznych). Struktury wyrobów gotowych (specyfikacje wyrobów, wykazy części, BOM) oraz ich części ujmują strukturalną i ilościową strukturę wyrobów gotowych składających się z półfabrykatów zespołów, komponentów, części, elementów i materiałów. W rozwiązaniach zintegrowanych dane te można pozyskać z sytemu CAD. Zapisane w relacyjnej bazie danych, wskazują ile elementów nadrzędnych składa się na element podrzędny.
Dzięki kartotece TPP można uzyskać odpowiedź na szereg pytań, w szczególności na pytania:
Ile i jakich zespołów, podzespołów, części, surowców potrzeba na wyprodukowanie zadanej liczby wyrobów?
Ile i jakie wyroby gotowe można wyprodukować na podstawie danych zespołów, komponentów, części, materiałów?
W jakich wyrobach, podzespołach występuje dany element, podzespół, materiał ? (pytanie nawiązujące do inwersyjnego wykazu części).
Drugą, równie ważną, kartoteką jest kartoteka przebiegu operacji procesów wytwarzania, inaczej kartoteka marszrut technologicznych. Kartoteka ta wskazuje, jakie operacje, w jakiej kolejności, na jakich grupach stanowisk (maszynach, stanowiskach roboczych) i przez pracowników, o jakich kwalifikacjach, muszą zostać wykonane, aby wyprodukować dany wyrób. Dane podawane są w układzie statycznym. Oznacza to, że nie jest definiowana konkretna maszyna o konkretnym numerze seryjnym, determinowana jest natomiast grupa maszyn technologicznie podobnych, tzn. zbiór maszyn mogących wykonać daną operację w zadanym czasie. Podobnie rzecz się ma z pracownikami. W kartotece przebiegu operacji konkretnego pracownika nie są definiowane jego dane osobowe, specyfikowane są tylko jego kwalifikacje, stawki pracy. Dobór maszyn i pracowników odbywa się na poziome zarządzania operacyjnego.
W ogólnym przypadku dla danego wyrobu może wystąpić kilka alternatywnych marszrut. Oznacza to, że odpowiednia kartoteka marszrut powiązana jest bezpośrednio z kartoteką operacji technologicznych stanowiącą swego rodzaju słownik. Kartoteka operacji technologicznych korzysta, z kolei z kartoteki stanowisk, grup maszyn, kartoteki kwalifikacji pracowniczych i kartoteki indeksów elementów, materiałów. Spróbujmy się zastanowić na ile tego rodzaju dane mogą być pozyskane z systemów CAD/PLM.
Dwa odrębne światy: Inżynier konstruktor i systemy CAD oraz inżynier procesu - ERP
Niestety, obecnie w bardzo wielu przypadkach świat inżyniera konstruktora a świat inżyniera procesu to dwa odrębne światy. Zazwyczaj wykorzystują niezależne narzędzia do wykonania swoich zadań. Chociaż istnieje duża analogia pomiędzy danymi z tabelki rysunkowej rysunku konstrukcyjnego, a strukturą BOM w ERP, to dane te są zazwyczaj przepisywane ręcznie pomiędzy systemami. Integracja pomiędzy tymi dwoma obszarami sprowadza się do operatora, tłumaczącego język konstruktora na język bazodanowy systemu ERP. Problem w tym, że konstruktor posługuje się rysunkiem, a ERP rozumie tylko indeks i operator dokonuje tłumaczenia z oznaczeń rysunkowych i przypisania na BOM indeksów zakupowych oraz założenia w ERP indeksów elementów projektowanych. Istnieją pewne funkcjonalności kluczowe dla systemów CAD/PDM i dla ERP. Na rysunku poniżej przedstawiono obszary funkcjonalności charakterystyczne dla „obu światów”.
Zakłada się, że ERP jest odpowiedzialny za tworzenie i zarządzanie bazą indeksów zakupowych, projektowanie struktur i procesów wytwarzania, zarządzanie procesami wytwarzania oraz kalkulacje koszów planowanych i rzeczywistych wytworzenia wyrobów. Z drugiej strony CAD/PDM jest odpowiedzialny za fazę projektowania wyrobu, półproduktów, strukturę konstrukcyjną. Obszar zarządzania zmianami dotyczy zarówno sfery CAD (zmiany konstrukcyjne), jak i ERP (zarządzanie zmianami wynikającymi z procesów wytwarzania). Współcześnie wymaga się również dostępu do danych zarządzanych przez zarówno przez ERP, jak i CAD. CAD/PDM powinien mieć dostęp do kartoteki indeksów zakupowych (wraz ich istotnymi atrybutami, np. ceną zakupu) oraz do koszów w fazie ofertowania oraz powykonawczych. Z kolei dla ERP pożądany byłby dostęp do aktualnej dokumentacji CAD oraz struktury konstrukcyjnej.
Tak jak ERP nie jest i prawdopodobnie nie będzie podstawowym narzędziem pracy konstruktora, tak nie zakłada się, że CAD/PDM zastąpi ERP.
Kluczowym elementem integracji jest indeks. ERP jest mało tolerancyjny w tym zakresie: aby mógł działać, należy jednoznacznie zidentyfikować surowiec, wyrób i podzespół. Rolę tę pełni indeks. Problem w tym, że mamy do czynienia z dwoma źródłami pochodzenia indeksu. Indeks elementów zakupowych pochodzi od ERP, a dla wyrobu czy też projektowanego elementu źródłem pochodzenia będzie projekt konstrukcyjny. Problem w tym, że indeksy maja tendencję do nadmiernego mnożenia i w związku z tym należy nad nimi panować w sposób efektywny. Zapanowanie nad indeksami to dobry pomysł na ich tworzenie i zarządzanie. Pomysł możliwy do realizacji w Rekord.ERP to zastosowanie klasyfikatora dla pozycji zakupowych. Indeks składa się z części klasyfikującej i identyfikującej obejmującej kolejnych przedstawicieli danej grupy.
Dla pozycji projektowanych, których źródło tkwi w CAD, pomysł na indeks jest związany z oznaczeniami rysunkowymi i rewizjami. Dodatkowo, dla przejrzystości indeksu, można zastosować separatory, sufiksy i prefiksy.
Pozycje zakupowe
nadawanie indeksu z wykorzystaniem klasyfikatora (źródło tkwi w ERP)
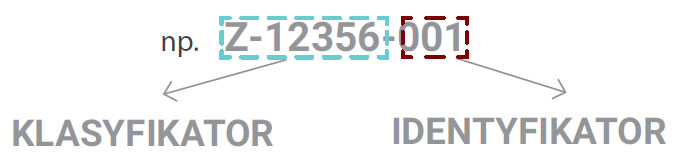
Pozycje projektowe
numer rysunku + wersja rysunku (możliwe prefiksy, sufiksy i separatory) ( źródło tkwi w CAD)
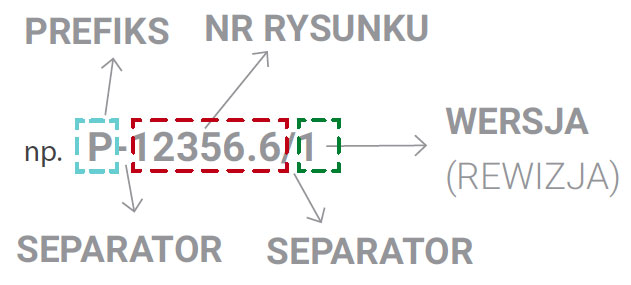
Modele integracji CAD/PDM z Rekord.ERP
Obecnie, w systemie Rekord.ERP można zastosować 3 podstawowe modele integracji. Poniżej podano założenia, wady i zalety w poszczególnych rozwiązaniach.
Model A
W modelu A trudno mówić o głębokiej integracji. Jest ona bardzo uboga. Założenia:
- praca na przynajmniej 4 ręce,
- po zatwierdzeniu dokumentacji przez konstruktora następuje skanowanie dokumentacji,
- nadawanie indeksów i podpięcie pod kartotekę rysunków w module TPP (techniczne przygotowanie produkcji),
- ręczne wprowadzenie struktury konstrukcyjnej do ERP (z tabelki rysunkowej).
Zaletą jest weryfikacja. Osoba wprowadzająca ręcznie struktury do systemu może jednocześnie weryfikować projekt - przynajmniej teoretycznie. Do tego modelu ostatnio wprowadzono funkcjonalność w module TPP pakietu Rekord.ERP związaną z możliwością korekty lokalizacji pliku. Jest to szczególnie pożądana funkcjonalność w firmach pracujących na dokumentacji obcej (pozyskanej od odbiorcy).
Model B
W modelu B pracochłonność prac została znacznie zmniejszona. Nie ma osoby przepisującej dane pomiędzy CAD a ERP. Zarządzanie tym procesem zostało przeniesione na konstruktora.
Założenia:
- praca na 2 ręce,
- po zatwierdzeniu dokumentacji przez konstruktora utworzenie dokumentacji 2D
- zapis plików w lokalizacji „archiwum dokumentacji”,
- wysłanie listy części z CAD do pliku *.xls,
- aplikacja „Integrator CAD” realizująca następujące zadania:
- z pliku *.xls wyczytuje listę części, powinny być podane indeksy ostatniego poziomu),
- może zakładać indeksy elementów projektowanych wg założonego „pomysłu” na indeks,
- przeszukuje katalogi archiwum dokumentacji umieszczonej na dysku, tworząc powiązanie pomiędzy indeksem, a plikiem rysunkowym.
Ten model jest dosyć obiecujący. Posiada jednak kilka wad. Wady tego rozwiązania to:
- konstruktor musi pamiętać o aktualizacji przy rewizjach,
- występuje duplikacja dokumentacji,
- dwa systemy połączone akcyjnie przez pliki.xls.
Model C
Model C pozbawiony jest wad modelu B, niemniej jednak wymaga dodatkowych narzędzi dostępnych z poziomu aplikacji CAD. Do tej pory wdrożono rozwiązanie wykorzystujące SEDI.ERP. Multikonektor firmy Solid Expert.
Założenia
- Praca wtyczki do aplikacji CAD realizująca następujące funkcjonalności:
- dostęp „on line” do bazy danych Rekord.ERP umożliwiający dodanie atrybutu indeksu zakupowego do karty obiektu CAD,
- przy zatwierdzeniu dokumentacji przez konstruktora i utworzeniu dokumentacji 2D przesłanie do bazy Rekord.ERP informacji o BOM (odpowiednio zaindeksowanej) i informacji o utworzonej dokumentacji 2D jak i modelu 3D,
- konstruktor z poziomu wtyczki ma dostęp „on line” do aktualnej kartoteki stanów magazynowych, MRP i kosztach.
- Praca bezobsługowa integratora wewnątrz systemu REKORD.ERP realizującego następujące funkcjonalności:
- zakładanie indeksów elementów projektowanych,
- zakładanie powiazania indeks – plik rysunkowy oraz model 3D,
- zktualizacja info o aktualnej wersji rysunkowej,
- automatyczne budowanie BOM.
Zakłada się dostęp do dokumentacji CAD, a nie jej duplikowanie. Dostęp do dokumentacji jest możliwy za pomocą usługi stworzonej przez f-mę REKORD SI zapewniającej również monitorowanie procesu dostępu do dokumentacji.
Wdrożony model C umożliwia wydajne wspomaganie procesu projektowania procesów wytwarzania. Technolog, mając do dyspozycji w module TPP strukturalną dokumentację konstrukcyjną, może w łatwy sposób ją przeglądać, posługując się modelem 3D oraz przeglądarką do modeli (np. eDrawings), poruszając się wprost po strukturze wyrobu. Operator może przechodzić po strukturze wyrobu i pokazywać rysunki na bieżąco.
Kolejną zaletą głębokiej integracji z systemami CAD/PDM jest możliwość wykorzystania dokumentacji w obszarze warsztatu produkcyjnego. W REKORD.ERP wprowadzono dostęp do dokumentacji konstrukcyjnej wykorzystującej technologię usługową. Usługa u_pliki współpracuje z tradycyjną rejestracją operacji, jak i panelem stanowiskowym. Dla warsztatu forma nieedytowalnej dokumentacji (np. pdf) jest najbardziej pożądaną. W celu przeszukiwania repozytorium dokumentacji może być wykorzystywana technika kodów kreskowych.
Systemy CAD - modele zastosowań
Jeden z najistotniejszych problemów początkowej fazy wdrożenia, jakim jest akwizycja danych struktur wyrobów oraz dokumentacji konstrukcyjnej, został znacznie zautomatyzowany. Firmy, w zależności od własnej specyfiki, mogą decydować się na rozwiązania od najbardziej uproszczonych prezentowanych w modelu A do najbardziej zaawansowanych prezentowanych w modelu C.
Model C jest najbardziej zaawansowanym - wymaga jednak w wielu przypadkach zmiany podejścia do organizacji procesu konstrukcji wyrobu. Nakłady w początkowej fazie polegające na mapowaniu obiektów CAD do indeksów materiałów zakupowych zwracają się w codziennej pracy działu konstrukcyjnego. W niedalekiej przyszłości będzie to wariant dominujący. Wdrożenie modułu TPP będzie można rozpoczynać od głębokiej integracji z modułami CAD. Wszystkie z wymienionych modeli zostały wdrożone w praktykę produkcyjną. Model C wykorzystuje f-ma Seco/Warwick – czołowy producent i przede wszystkim projektant zaawansowanych urządzeń do obróbki cieplnej. W okresie 3 miesięcy zostało przesłanych ok. tysiąca sesji projektów zawierających kilka tysięcy pozycji struktur wyrobów. Na chwilę obecną wydaje się, że model C posiada największy potencjał do realizacji zarówno w chili obecnej jak i w niedalekiej przyszłości.