Wdrożenie ERP w Zakładzie Wyrobów Metalowych STRUMET Sp. z o.o.
Strumet jest jednym z największych w Europie producentów systemów transportu i magazynowania części i podzespołów samochodowych. Firma powstała w 1995 roku. Klienci Strumetu to największe koncerny motoryzacyjne i poddostawcy branży automotive. Produkty firmy służą do bezpiecznego i efektywnego transportu pomiędzy zakładem poddostawcy, a zakładem finalnego montażu samochodów. Najczęściej są to specjalistyczne pojemniki projektowane dla konkretnego podzespołu, np. silnika, zderzaka, szyby itp.
Dział produkcji Strumetu wyposażony jest w nowoczesne urządzenia, m. in. pięć laserowych ploterów do cięcia blach, trzy urządzenia do laserowego cięcia rur, dwa plotery do plazmowego cięcia blach, trzy frezerskie centra obróbcze oraz stanowisko do sterowanego cyfrowo gięcia rur. W Strumecie pracują trzy zrobotyzowane stanowiska spawalnicze firmy Comau. Firma dysponuje również własnym biurem konstrukcyjnym, wyposażonym w oprogramowanie CATIA V5, Autodesk Inventor, AutoCad, Esprit i NX Siemens. Wydział Ocynkowni Ogniowej Zakładu Strumet świadczy usługi cynkowania konstrukcji stalowych. Ocynkownia została wyposażona w jedną z największych w Polsce wanien z ciekłym cynkiem.
Około 90 procent produktów Strumetu jest eksportowana. Produkty wysyłane są do większości krajów Europy, a w ostatnich latach także do Afryki Południowej oraz Ameryki Północnej i Południowej.
Początki współpracy, czyli decyzja o wdrożeniu systemu zarządzania produkcją
Początek współpracy między Strumetem a firmą REKORD SI to koniec roku 2013. Po serii prezentacji i negocjacjach, dokonano wyboru ERP, a w lutym 2014 roku została podpisana umowa na dostawę, instalację i wdrożenie systemu informatycznego Rekord.ERP. Oczywiście pierwszym etapem wdrożenia ERP było opracowanie studium wdrożeniowego, w ramach którego dokonano szczegółowej analizy procesów realizowanych w Zakładzie Wyrobów Metalowych Strumet oraz opracowano model funkcjonowania systemu REKORD.ERP w firmie.
Podstawowe obszary poddane analizie związane były z:
- obsługą klienta (ewidencja ofert, obsługa zamówień od klientów, obsługa wysyłek i sprzedaży),
- wytwarzaniem wyrobów (moduł Technicznego Przygotowania Produkcji, emisja zleceń, dokumentacja warsztatowa, planowanie, monitorowanie procesu produkcyjnego, rejestracja wykonania produkcji, rejestracja niezgodności w procesie produkcyjnym, rozliczenie kosztów produkcji),
- logistyką (zaopatrzenie, obrót materiałowy oraz wyrobów gotowych),
- finansami,
- rozliczeniem kosztów,
- obszarem kadrowo-płacowym.
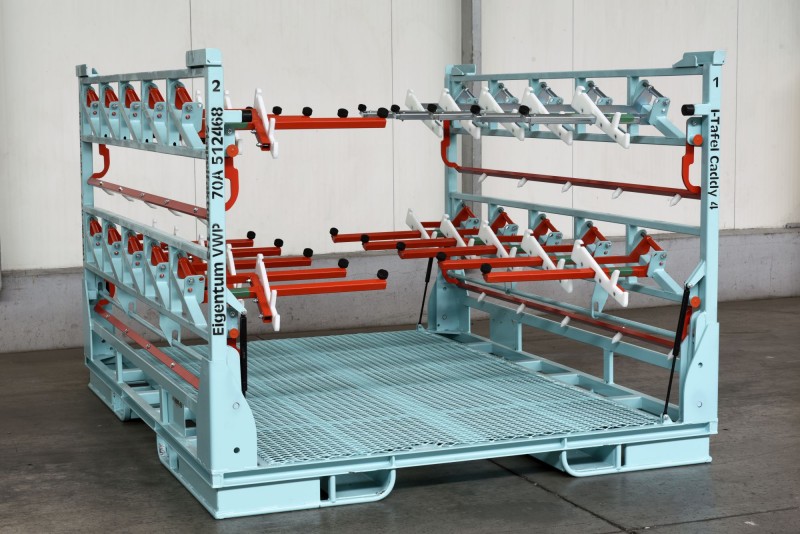
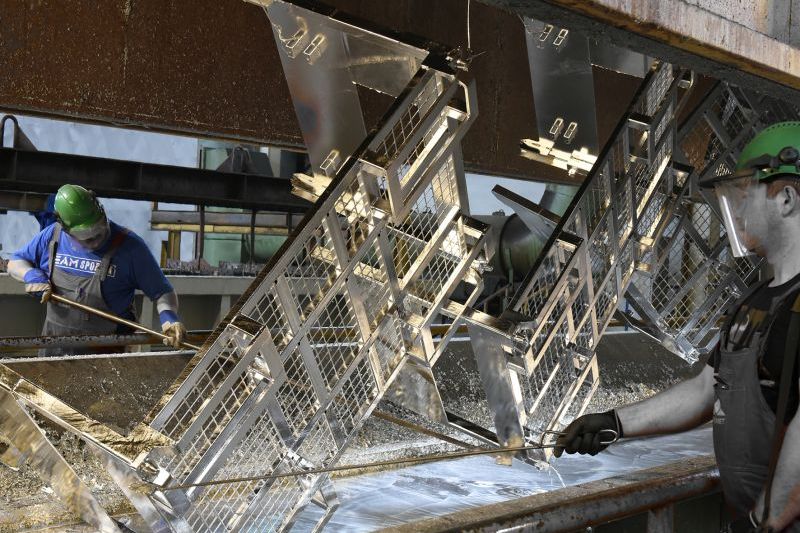
Po zakończeniu studium, w lipcu 2014 roku, rozpoczęły się właściwe prace związane z wdrożeniem ERP. Na początku prace dotyczyły budowy bazy wiedzy, opracowania struktur wyrobów i procesów technologicznych (m. in. opracowano dedykowane mechanizmy obliczania norm zużycia wybranych materiałów oraz wizualizacji i edycji operacji technologicznych), tworzenia kalkulacji ofertowych oraz fakturowania.
Olaf Sznapka, prezes zarządu w Zakładzie Wyrobów Metalowych Strumet Sp. z o. o.: Przy wyborze systemu kierowaliśmy się między innymi tym, że system Rekordu można dostosować do specyficznych procesów naszej firmy. Po ich zamodelowaniu możemy je zabezpieczać przed błędami we wprowadzaniu danych przez naszych pracowników. Taką samą funkcjonalność możemy stosować do źródłowych procesów systemu Rekord po wcześniejszym przeprowadzeniu konsultacji i testów Możliwość zatrudnienia absolwentów bielskiego ATH (z czego oczywiście skorzystaliśmy), którzy na zajęciach poznają system Rekord.ERP, było również elementem wpływającym na wybór tego produktu.
Jak planować produkcję?
Kolejnym etapem wdrożenia ERP było uruchomienie zleceń wytwarzania wyrobów gotowych na podstawie zarejestrowanych zamówień oraz wdrożenie modułu gospodarki magazynowej. Pozwoliło to usprawnić proces planowania potrzeb materiałowych. Następnie uruchomiono zlecenia na detale oraz rejestrację operacji. W styczniu 2015 roku rozpoczęto pełną rejestrację faktur, dokumentów obrotu magazynowego i pracę w obszarach finansowo-księgowych i kadrowo-płacowych.
Początkiem roku 2016 został podpisany protokół zakończenia pierwszego etapu wdrożenia, który obejmował wdrożenie pełnej funkcjonalności modułów wchodzących w skład pakietów finansów i zasobów ludzkich, pełnej obsługi procesów logistycznych (zaopatrzenie, gospodarka magazynowa w obszarze materiałów i wyrobów gotowych) i obsługi klienta (ofertowanie, zamówienia i fakturowanie) oraz obsługę podstawowego zakresu obsługi zleceń wytwarzania.
Sporym wyzwaniem była obsługa procesu wytwarzania. Główne procesy obróbkowe w przedsiębiorstwie to przygotowanie materiału (cięcie, gięcie, obróbka skrawaniem na maszynach CNC), spawanie, cynkowanie, lakierowanie proszkowe oraz montaż. Jednak to nie one stanowiły problem. Największym wyzwaniem była organizacja procesu wytwarzania i logistyka przepływów materiałów, detali, półwyrobów i wyrobów gotowych oraz bardzo rozbudowany i dynamiczny proces kooperacji na różnych etapach powstawania wyrobu.
Optymalizacja ERP
Głównym efektem wdrożenia ERP jest osiągnięcie bardzo dużej złożoności wyrobów - wielopoziomowych struktur, które wynikają ze złożoności procesu wytwarzania i dużego udziału operacji wykonywanych w kooperacji na różnych etapach procesu. Przekłada się to na wielopoziomową strukturę powiązanych ze sobą zleceń wytwarzania. Warunki te wymusiły zastosowanie innowacyjnego podejścia do kooperacji, w którym zadania (operacje) wykonywane poza przedsiębiorstwem obsługiwane są przez odrębne zlecenia.
Olaf Sznapka: Wdrożenie oprogramowania to proces, który jeszcze będzie trwał długo, ale już teraz udało się nam obniżyć stan zapasów magazynowych materiałów zakupowych. Poprzez wprowadzanie systemu lokalizacji na magazynach półproduktów i detali oraz w tzw. strefach przy produkcyjnych (strefa buforowa przed magazynowaniem) przyspieszone zostały procesy przygotowania materiałów wysyłanych do kooperacji oraz do wydziałów spawalni i montażu. Uruchomienie automatycznego rozchodu materiałów z magazynów produkcyjnych dla wydziałów CNC oraz obróbki mechanicznej pozwoliło ograniczyć wielkość odpadu nie użytkowego. Wiele procesów organizacyjno-technicznych, takich jak np. ciągła weryfikacja technologii realizowanych jest przez zabezpieczenia systemowe. Rejestracja operacji na wszystkich wydziałach produkcyjnych, w tym także kooperacji, pozwoliła nam uporządkować proces produkcji, a to przekłada się na zwiększenie wydajności czyli na większe korzyści ekonomiczne.
Wdrożenie ERP w firmie STRUMET realizowane było w sposób ewolucyjny. Mimo przeprowadzonej analizy przedwdrożeniowej, w trakcie wdrożenia na bieżąco dostosowywano procesy do potrzeb firmy. Pewne pomysły wypracowane w studium nie obroniły się w rzeczywistych warunkach produkcyjnych. Dopiero na etapie wdrożenia, wiele procesów okazało się znacznie bardziej skomplikowanych niż przy pierwszych analizach. W związku z tym niektóre rozwiązania były weryfikowane na bieżąco w trakcie pracy i ulegały zmianom podczas optymalizacji ERP.
Obecnie, zgodnie ze znaną prawdą, że "wdrożenie systemu informatycznego, wspomagającego zarządzanie przedsiębiorstwem nigdy się nie kończy" - tak jak nie kończą się działania związane z doskonaleniem procesów w przedsiębiorstwie - realizowana jest ciągła współpraca między firmami REKORD SI i STRUMET w zakresie coraz lepszego wykorzystywania systemu Rekord.ERP podczas zarządzania produkcją w fabryce.
Grzegorz Gunia, specjalista ds. wdrożeń w Rekord SI
Marek Kasztura, koordynator ds. wdrożenia